近年来,机床制造基础和共性技术研究不断加强,产品开发与技术研究同步推进。机床产品的可靠性设计与性能试验技术、多轴联动加工技术等多项关键技术的成熟度有了很大提升。数字化设计技术研究成果在高精度数控坐标撞床、立式加工中心等产品设计上进行实际应用;多误差实时动态综合补偿和嵌入式数控系统误差补偿等软硬件系统在多个企业、多个产品上进行了示范应用,使数字控制机床精度得到了明显提升。无需任何中间转换装置实现电能向直线运动机械能的直接转换,就是直线电机,结构简单、磨损少、效率高、噪音小以及组合性强是其主要的优势。交流直线电机是当前在高精度数字机床上普遍应用的设备,这种设备有直线感应电机和永磁直线同步电机两种,直线感应电机成本较低,并且受到外界干扰影响的程度较低,同时也可以抗电磁干扰;永磁直线同步电机同时具备直线电机和永磁电机的优势,响应速度更快、体积更小、推力能量更大,所以是当前高精度直线进给系统的首选。
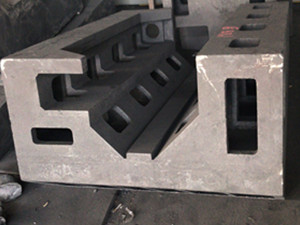
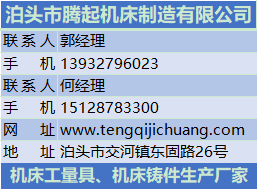
导轨材料的优化,通过开发新材料,改善滚动体性能从而提升导轨的耐磨性,可延长导轨使用寿命;在静压导轨中,介质可更换为水源、空气等,实现节能环保、绿色生产的同时更能节约生产成本,提高数控机床铸件生产效益。
二、数控加工机床的产生演进
科学技术和社会生产力的迅速发展,数控加工机床(NumericalControlMachineTools)是用数字代码形式的信息(程序指令),控制刀具按给定的工作程序、运动速度和轨迹进行自动加工的机床,简称数控加工机床。
数控加工机床是在机械制造技术和控制技术的基础上发展起来的,其过程大致如下:
1948年,美国提出采用数字脉冲控制机床的设想。
1952年试制成功第一台三坐标数控铣床,当时的数控装置采用电子管元件。
1959年,数控装置采用了晶体管元件和印刷电路板,出现带自动换刀装置的数控加工机床,称为加工中心(MC,MachiningCenter),使数控装置进人了第二代。
1965年,出现了第三代的集成电路数控装置,不仅体积小,功率消耗少,且可靠性提高,价格进一步下降,促进了数控加工机床品种和产量的发展。
上世纪60年代末,先后出现了由一台计算机直接控制多台机床的直接数控系统(简称DNC),又称群控系统;采用小型计算机控制的计算机数控系统(简称CNC),使数控装置进人了以小型计算机化为特征的第四代。
1974年,研制成功使用微处理器和半导体存贮器的微型计算机数控装置(简称MNC),这是第五代数控系统。
上世纪80年代初,随着计算机软、硬件技术的发展,出现了能进行人机对话式自动编制程序的数控装置;数控装置愈趋小型化,可以直接安装在机床上;数控加工机床的自动化程度进一步提高,具有自动监控刀具破损和自动检测工件等功能。
上世纪90年代后期,出现了PC+CNC智能数控系统,即以PC机为控制系统的硬件部分,在PC机上安装NC软件系统,此种方式系统维护方便,易于实现网络化制造。
泊头市腾起机床制造有限公司(http://www.tengqijichuang.com)是一家致力于机床量具、机床铸件产品生产、销售为一体的现代化企业。可定做各类机床横梁铸件、机床滑枕铸件、机床导轨铸件等,产品远销多个省、市、自治区。